Benefits of MDR Diverts & Merges
Whether it be mis-diverts, jams, spilled totes, or crushed boxes, these are things that cost time, labor, and reduce orders On-Time & In-Full (OTIF). Having a consistent and quality flow of totes and cases is important to sustaining the processes that create throughput within every distribution and fulfillment operation.
Our Series 1500 MDR product line offers MDR Diverts & Merges to help protect your bottom line and customer satisfaction.
MDR Diverts & Merges compared to the traditional:
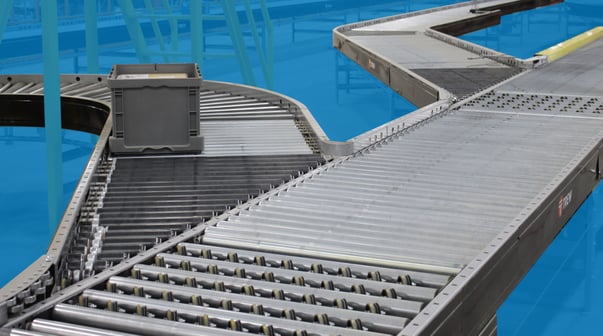
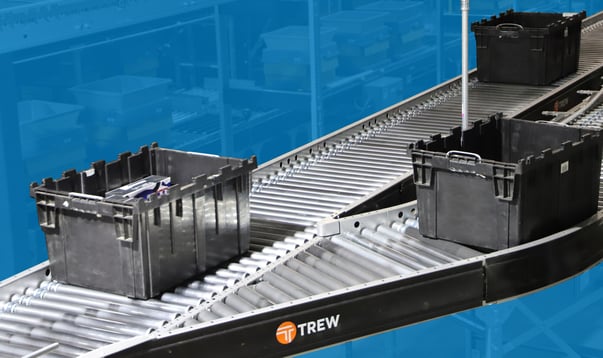
- Energy Efficiency: MDR technology uses motorized rollers for on-demand operation, reducing energy consumption and system wear.
- Precise & Gentle Handling: MDR diverts & merges offer precise control for smoother item handling, reducing jams and misalignments.
- Reduced Maintenance: Modular MDRs have fewer moving parts, resulting in lower maintenance and increased productivity.
- Quiet Operation: MDR technology produces less noise, making it suitable for noise-sensitive work environments.
- Flexible Layouts: Easily adapt to changing production needs and floor plans, enhancing conveyor design versatility.
- Space Saving: MDR diverts & merges are more compact, optimizing floor space in warehouses and production facilities.
- Belt Tracking Elimination: MDR Merge systems eliminate complex belt tracking, reducing maintenance efforts and improving system reliability.
- Accurate Merge Control: MDR Merge systems enable precise merging with synchronized motorized rollers, ensuring a seamless, collision-free merging process.
- Accumulation Capabilities: MDR technology includes built-in accumulation zones for improved flow control and efficiency.
- Faster Installation: MDR diverts & merges are quicker to install compared to traditional systems.
- Reduced Overall Cost: While initial costs may be higher, MDR technology leads to lower operating costs over time.