CX Spotlight - Spare Parts
If you’re like most companies, 2020 was one for the books. Not only are we having to remain fluid with the impacts of Covid-19 but talks about strategic plans and budgets for 2021 is requiring all of us to pull out our crystal balls.
There is one thing that all facilities should be doing right now in preparation for peak and it’s the easiest way to avoid unplanned downtime at your site: ensuring that you have spare parts in inventory to support your system.
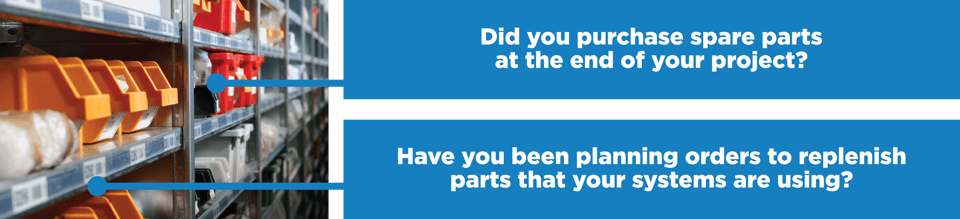
When your system was new, you may have started with a well-stocked parts cage. Over time, whether it was due to budgets or oversight, it'ss just natural for parts to be used and never re-ordered and eventually, inventories are not at the levels they should be. As your systems age, it’s more important than ever to have a well-stocked inventory of spares, as components wear and are more prone to failure during its normal lifecycle.
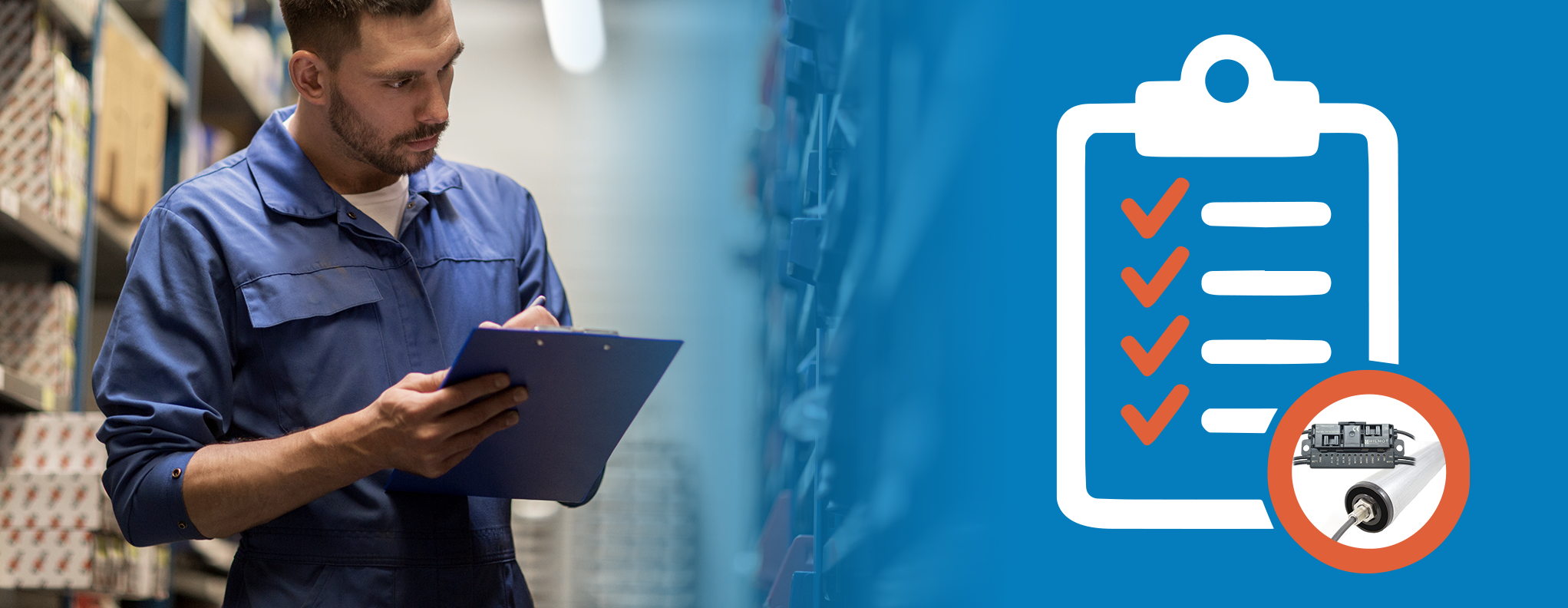
To help, TREW has provided some items to consider for parts management best practices to help you get your spares on track. These are easy things you can do every year to make sure you can minimize downtime if issues occur at your site.
- Check to make sure you have your original recommended spare parts list(s). If you don’t, reach out to obtain your lists. Make sure you have your job number or the name of your facility at the time the equipment was installed. Ask them to update the pricing and whether or not the part is stocked so you can use these decisions to determine which parts need to be physically on your shelf.
- Take inventory of what you have on your shelves. Identify inventory locations and label them with magnets so you have future flexibility to re-arrange your parts cage as your needs change. Record the locations on a spreadsheet or in your CMMS/EAM along with the quantities that you have at that moment.
- Compare what you have to what was originally recommended on your spares list. Adjust your quantities to reflect what you’ve been experiencing thru actual usage but also make sure you have at least one of each component on your shelf or have a plan to get it the same day or next if you have a limited budget. Order what you need or plan to restock your parts cage over time as budget becomes available.
- Take this opportunity to organize your parts cage. Throw out used parts or any parts that you don’t know what they are used for. A little hint: Don’t group like parts together so it'ss difficult for someone to come and take what they need without checking out the parts the proper way.
- Train your other maintenance staff on how to properly check in and check out parts. If you keep this process in place, monthly cycle counting is all you need to trust your inventory. Reinforce your processes on at least a quarterly basis.
- Take a “Walk, Look, Listen” of your critical path and components. Make sure you have spares for any areas that may be unusually noisy or where you may see shavings/oil. Or better yet, go ahead and change out these components in advance of a failure.
If everyone had a crystal ball, it would be easy to plan for unexpected component failures. But since no MHE provider has developed such a crystal ball yet, the best way to minimize outages is to plan and have your spare parts on site.